Future Trends in Pelletization Equipment
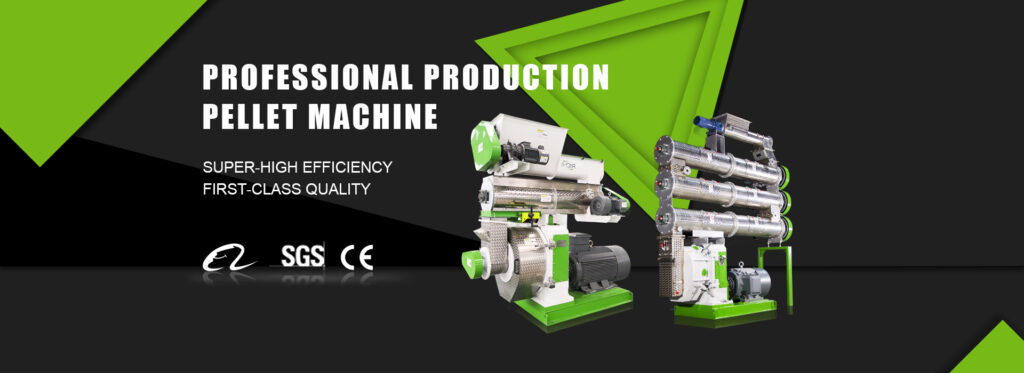
In the ever-evolving landscape of industrial processes, pellet mill machine plays a crucial role in transforming raw materials into valuable products. Whether in the pharmaceutical, food, or agriculture industries, pelletization is an essential step in creating uniform, easily transportable, and efficiently processed materials. Today, we will delve into the future trends of pelletization equipment, exploring how advancements in technology, sustainability, and automation are shaping this critical facet of manufacturing.
Increased automation of the pelletizing process
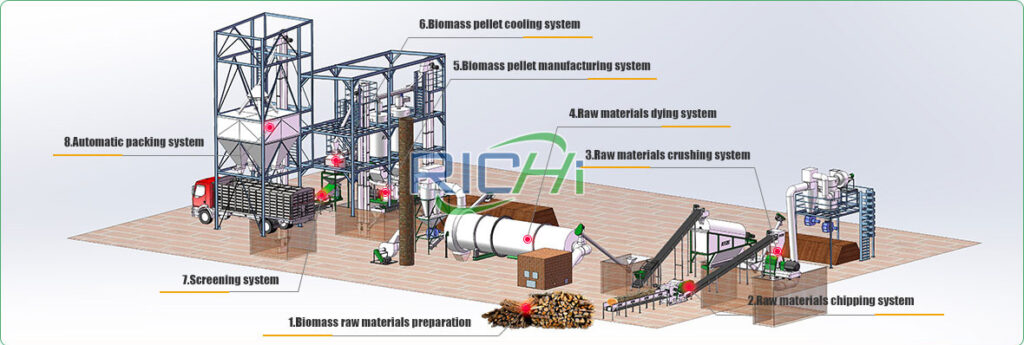
One of the primary reasons for the escalating automation of pelletizing is the quest for precision and consistency. Automation eliminates the variability introduced by human operators. Modern automated systems can meticulously control factors like pellet size, shape, and quality, resulting in products of superior uniformity.
Industries today face ever-growing demands for their products. The manual or semi-automated processes of the past simply cannot keep up. Increasing automation in pelletizing allows manufacturers to scale up their production capacity efficiently, meeting the demands of a rapidly changing market.
Quality control is paramount in manufacturing, and automated pelletizing systems excel in this regard. Manufacturers can implement stringent quality control measures and trace the entire production process to ensure consistently high-quality pellets.
Automation isn’t just about the present; it’s also about preparing for the future. By embracing automation, manufacturers position themselves to adapt to upcoming technological advancements and industry trends. It ensures they remain competitive and relevant in a constantly evolving industrial landscape.
Utilizing environmentally friendly materials for pelletizing
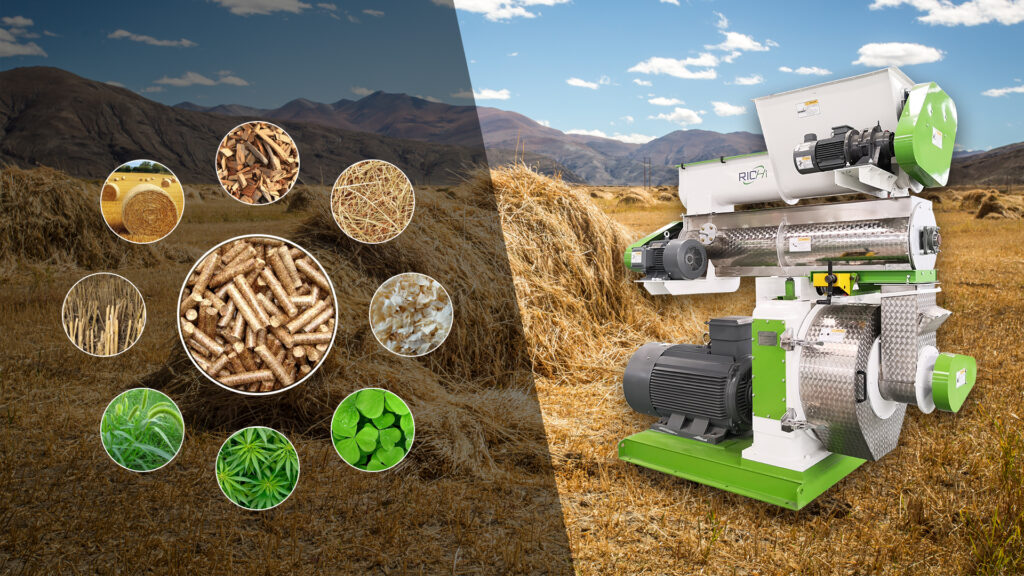
The adoption of environmentally friendly materials in pelletizing comes with a host of benefits. It significantly reduces the carbon footprint associated with traditional materials. Moreover, it helps in curbing the growing menace of plastic waste by utilizing biodegradable and recyclable alternatives.
Biodegradable polymers, often derived from renewable sources, are emerging as a sustainable alternative in pelletizing. They find applications in various industries, including packaging and agriculture, and are compostable, reducing the burden on landfills.
Recycling plays a pivotal role in sustainable pelletizing. Incorporating recycled materials, such as post-consumer plastic waste, not only reduces waste but also conserves energy and resources.
Agricultural residues, such as rice husks and corn stalks, can be utilized in pelletizing. By converting these waste materials into pellets, industries can reduce agricultural waste and create valuable products simultaneously.
Sustainable forestry practices ensure a continuous supply of wood and biomass for pellet production. These materials are renewable and contribute to the reduction of greenhouse gas emissions when used as an alternative to fossil fuels.
Customizable pelletizing production process
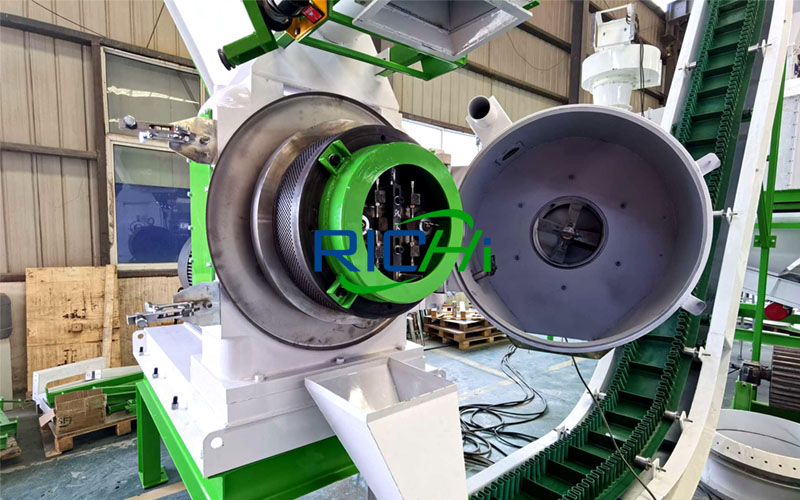
Model | MZLH320 | MZLH350 | MZLH420 | MZLH520 | MZLH768 | MZLH858 |
---|---|---|---|---|---|---|
Anti-caking Feeder Power | 1.5KW | 1.5KW | 1.5KW | 2.2KW | 3KW | 3KW |
Forced Feeder Power | 0.55KW | 0.55KW | 0.55KW | 0.75KW | 1KW | 1KW |
Pellet Machine Power | 37KW | 55KW | 110KW | 160KW | 250KW | 280KW |
Capacity(wood sawdust,biomass) | 300-400KG/H | 500-700KG/H | 1.0-1.2 T/H | 2.0-2.5 T/H | 2.5-4 T/H | 3-4.5 T/H |
Capacity(grass,straw) | 600-800KG/H | 800-1000KG/H | 1.5-2 T/H | 3-4 T/H | 5-7 T/H | 8-10 T/H |
Capacity(organic fertilizer) | 1-2 T/H | 3-4 T/H | 5-6 T/H | 7-8 T/H | 9-10 T/H | 10-12 T/H |
Final Pellet | 6-12mm | 6-12mm | 6-12mm | 6-12mm | 6-12mm | 6-12mm |
Weight(KG) | 2500 | 3500 | 4000 | 4500 | 5000 | 5500 |
Dimension(mm) | 2200*900*1300 | 2500*1100*1600 | 2800*1150*1730 | 3000*1260*1860 | 3300*1500*2000 | 3500*1600*2180 |
Industries today operate in a dynamic environment where flexibility and customization are essential. The realization that one-size-fits-all approaches may not suffice has led to the exploration of customizable pelletizing production processes.
The primary advantage of customization in pelletizing is the ability to meet unique product requirements. Whether it’s altering the composition of pellets or adjusting production parameters, customization ensures that the end product precisely aligns with industry needs. This not only maximizes efficiency but also enhances cost-effectiveness.
Customization begins with tailored formulations. Manufacturers can adjust the composition of pellets to meet specific requirements, whether it’s enhancing durability, altering chemical properties, or meeting certain industry standards.
The ability to produce pellets of varying sizes is a hallmark of customizable pelletizing. This versatility enables manufacturers to cater to a wide range of applications, from fine powders to large pellets.
Energy-saving technologies for pelleting machine
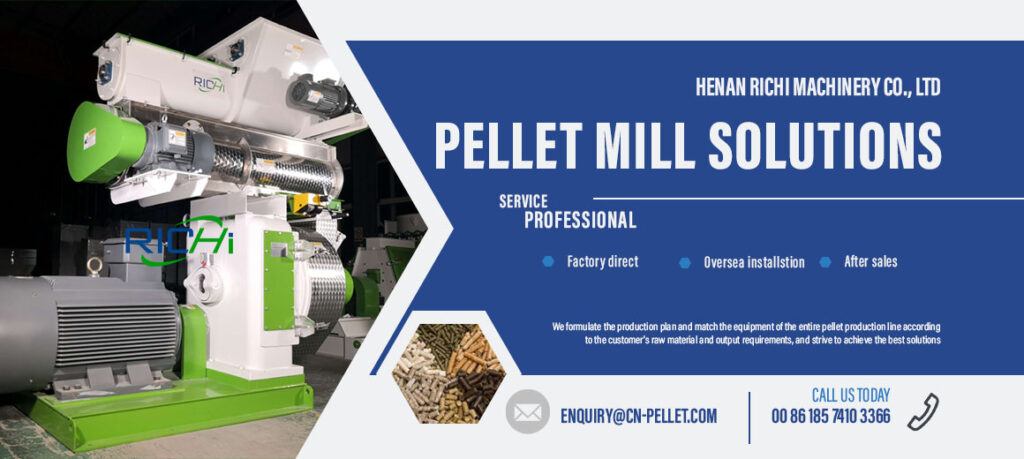
VFDs allow pelleting machines to adjust motor speed based on the required output. This prevents the machine from running at full power when it’s not necessary, resulting in significant energy savings.
Upgrading to high-efficiency motors can make a substantial difference in energy consumption. These motors are specifically designed to minimize energy loss through heat, making the pelleting process more efficient.
Upgrading to high-efficiency motors can make a substantial difference in energy consumption. These motors are specifically designed to minimize energy loss through heat, making the pelleting process more efficient.
Heat recovery systems capture the heat generated by the pelleting machine and reuse it for various purposes within the manufacturing facility, such as heating or drying. This reduces the need for additional energy sources.
Regular maintenance is often overlooked but is crucial for keeping pelleting machines operating at peak efficiency. Proper maintenance can prevent energy-wasting issues such as leaks, worn-out parts, and inefficient operation.
Digital real-time monitoring of pellet line
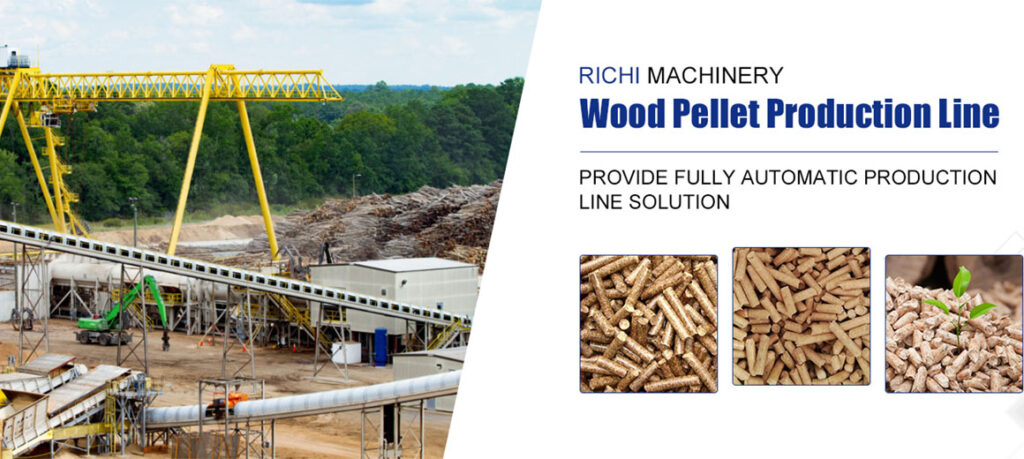
Sensors play a critical role in real-time monitoring. They collect data on various process parameters, such as temperature, pressure, and humidity, allowing operators to closely track the production process.
Data acquisition systems collect and process data from sensors in real-time. They transmit this data to a centralized monitoring and control system, providing operators with a comprehensive overview of the entire pellet production process.
SCADA systems offer real-time visualization of data and processes on a user-friendly interface. They also enable remote control and monitoring, allowing operators to make adjustments even when not physically present on the shop floor.
Cloud-based solutions provide the advantage of storing and analyzing data in the cloud. This data can be accessed securely from anywhere with an internet connection, enabling remote monitoring and data-driven decision-making.
Machine learning and predictive analytics are used to analyze the data collected in real-time. These technologies can recognize patterns and deviations, allowing for predictive maintenance and the prevention of costly downtime.
Pellet Production Line
Core Equipment of Wood Pellet Production Line
RICHI Pellet Machine For Sale
- Wood Pellet Mill For Sale
- Grass Pellet Making Machine For Sale
- Straw Pellet Machine For Sale
- Rice Husk Pellet Machine For Sale
- EFB Pellet Machine For Sale
- Organic Fertilizer Pellet Machine For Sale
- Cat Litter Pellet Making Machine For Sale
- Textile Cord Pellet Machine For Sale
- Paper Pellet Making Machine For Sale
- Pellet Maker For Pellet Stove