Advanced Pellet Production Line Solutions
Discover our advanced pellet production line solutions designed to meet the diverse needs of biomass pellet production. Our state-of-the-art pellet mill equipment offer unmatched efficiency and reliability, ensuring superior performance for your production requirements. Whether you are looking to produce biomass pellets from wood, straw, or other organic materials, our customizable and innovative systems are tailored to provide optimal results. Enhance your production capabilities and achieve sustainable, high-efficiency output with our comprehensive pellet production line solutions.
Why Choose Our Pellet Production Line?
01
Advanced Technology and Innovation
Our pellet production line is built using state-of-the-art technology and innovative designs. We incorporate the latest advancements in pelletizing equipment to ensure high efficiency, durability, and ease of operation.
02
Customizable Pellet Production Solutions
We understand that different customers have different needs. That’s why we offer customizable pellet production line solutions tailored to your specific requirements.
03
Comprehensive Support and Services
Choosing our pellet production line means you’re backed by a team of experienced professionals dedicated to ensuring your success:
04
Cost-Effective and Sustainable
Our pellet production lines are designed to be both economically and environmentally sustainable.
Key Features of Our Biomass Pellet Machine
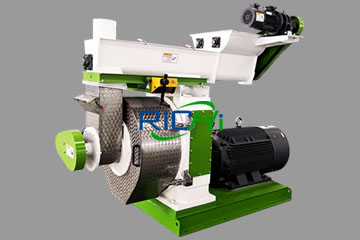
Our biomass pellet machines are engineered to deliver exceptional efficiency and performance, ensuring maximum output with minimal energy consumption. The advanced design and precision engineering of our machines allow for consistent and reliable pellet production, optimizing the use of raw materials and reducing waste. This high efficiency not only enhances productivity but also lowers operational costs, making it a cost-effective solution for large-scale biomass pellet production.
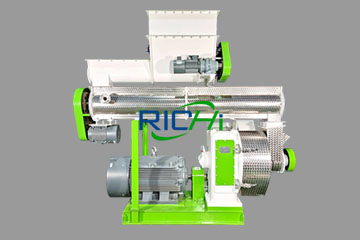
Built with high-quality materials and components, our biomass pellet machines are designed for long-term durability and robust performance. The heavy-duty construction ensures that the machines can withstand the rigors of continuous operation in demanding environments. Key parts such as the rollers, dies, and motors are made from wear-resistant materials, extending the lifespan of the machine and reducing maintenance requirements. This durability translates into reliable operation and minimal downtime, crucial for maintaining production schedules.
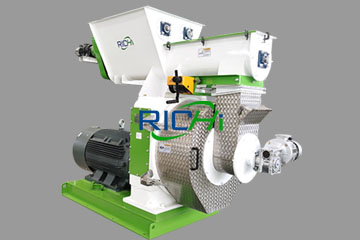
Our biomass pellet machines are versatile and can handle a wide range of biomass materials, including wood chips, sawdust, straw, rice husks, and other agricultural residues. The machines are equipped with adjustable settings that allow for customization based on the type and moisture content of the raw materials. This flexibility ensures optimal pellet quality and efficiency, regardless of the input material. Additionally, the machines can be easily integrated into existing production lines or configured for standalone operation, providing a flexible solution for various production needs.
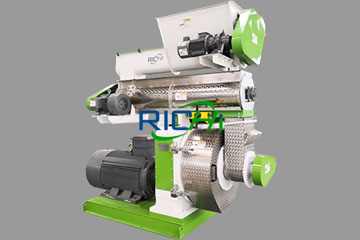
Ease of use is a key feature of our biomass pellet machines. The intuitive design and advanced control systems make operation simple and straightforward, even for operators with minimal training. The machines are equipped with user-friendly interfaces, allowing for easy monitoring and adjustment of key parameters such as temperature, pressure, and feed rate. Safety features and automated controls ensure smooth and secure operation, reducing the risk of errors and enhancing overall efficiency.
Comprehensive Pellet Mill Equipment Overview
A complete biomass pellet production line usually includes several links such as crushing, drying, pelletizing, cooling, sieving and packaging. The equipment in each link has specific functions and features to ensure that the whole production process is efficient, stable and environmentally friendly. By reasonably configuring these equipments, different scales and types of biomass pellet production needs can be met, realizing efficient production and high-quality products.
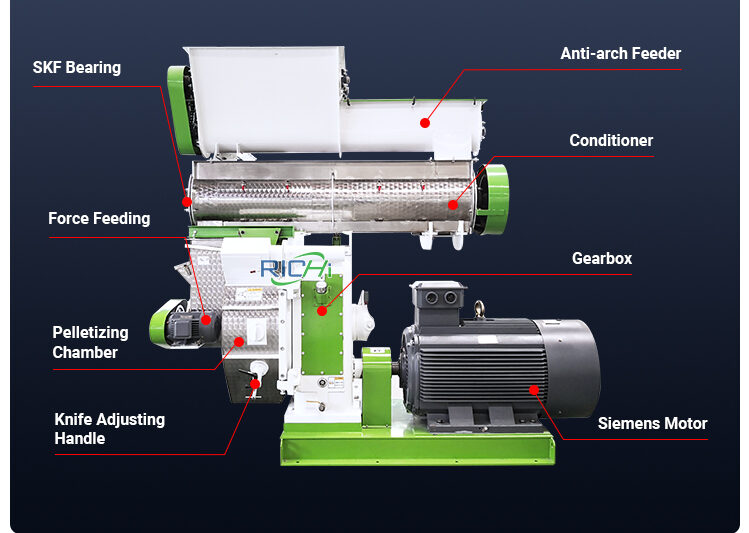
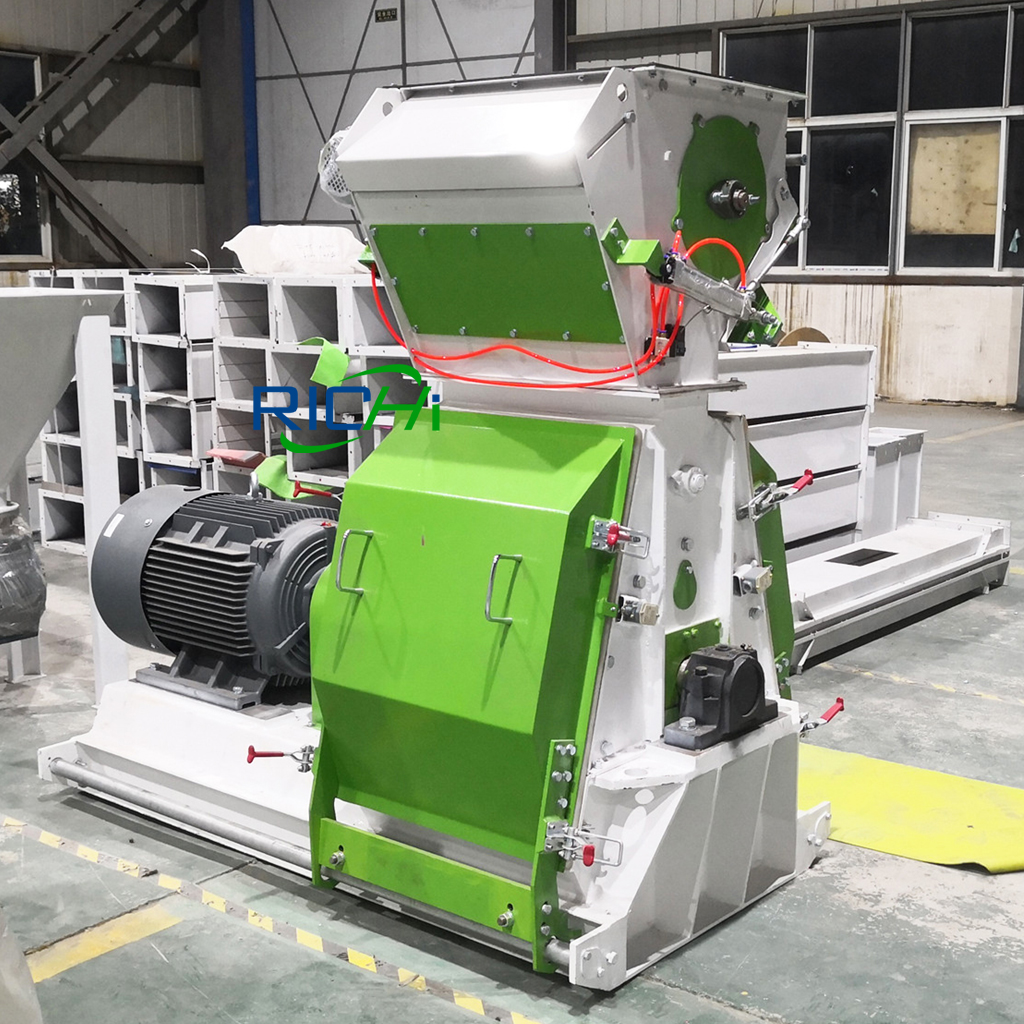
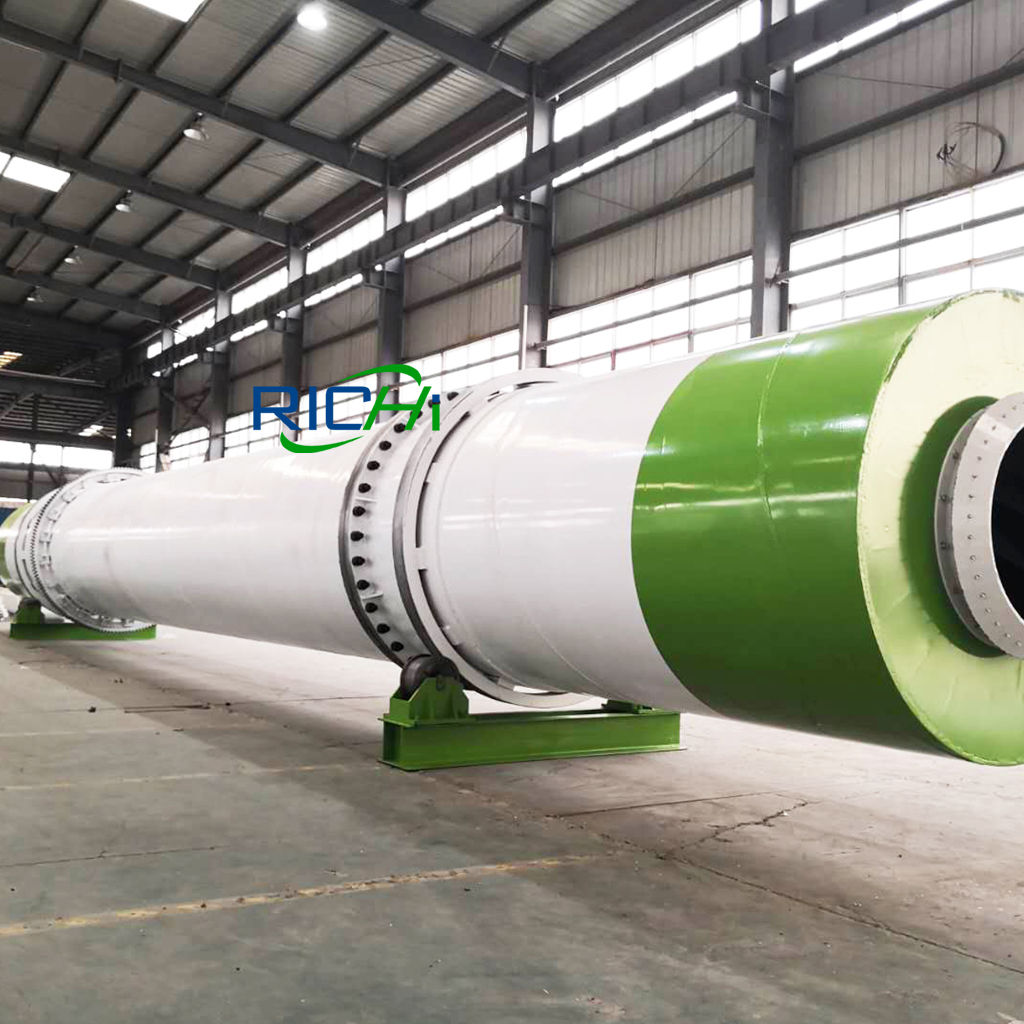
Brands We Partner With
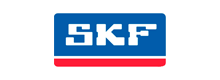
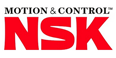
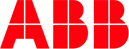

Pellet Production Line
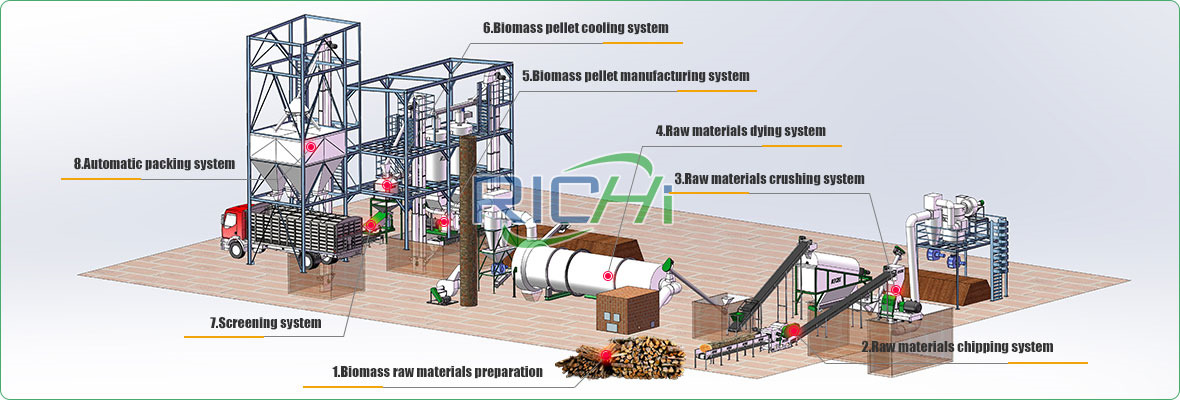
Complete pellet production line, customizable
The key determining factors in the design of the pellet production line, the production process and the configuration of the pellet mill equipment are the raw material and the production capacity. RICHI Machinery customizes the complete pellet plant according to the status of the raw material, the production capacity required and the size of the workshop on the site.
RICHI Machinery
Pellet production line guide
Setting up a pellet production line involves several key steps, from initial planning and site preparation to equipment installation and production start-up.
Initial Planning
Market Research
Supply Chain: Research the availability of raw materials (e.g., wood chips, sawdust, straw, agricultural residues) and potential suppliers.
Feasibility Study
Profitability Analysis: Estimate potential revenue, operational costs, and profit margins to ensure the project’s financial viability.
Site Selection and Preparation
Location
Utilities: Ensure the site has reliable access to electricity, water, and other necessary utilities.
Facility Layout
Safety and Compliance: Ensure the facility meets local safety regulations and environmental standards.
Equipment Selection and Procurement
Key Equipment
Dryer : For reducing the moisture content of raw materials.
Pellet Mill : For compressing the dried materials into pellets.
Cooler : For cooling down the hot pellets after production.
Sifter : For separating finished pellets from fines and ensuring uniform size.
Bagging Machine : For packaging the pellets into bags for storage and transport.
Vendor Selection
Technical Support: Ensure the vendor provides adequate technical support, including installation, training, and maintenance services.
Operational Training
Staff Training
Safety Protocols: Educate employees on safety procedures and emergency protocols.
Process Optimization
Process Monitoring: Use monitoring systems to track production parameters and optimize processes.
Production Start-Up
Initial Production Run
Trial Production: Conduct a trial production run to fine-tune the equipment settings and identify any issues.
Full-Scale Production
Adjustments: Make any necessary adjustments to optimize performance and output.
Quality Control and Assurance
Product Testing
Compliance: Ensure the pellets meet industry standards and customer specifications.
Continuous Improvement
Process Enhancements: Continuously enhance processes and equipment based on feedback and performance data.
Marketing and Sales
Branding and Promotion
Digital Marketing: Utilize digital marketing strategies, including social media, and online advertising, to reach potential customers.
Sales Channels
Customer Relationships: Build and maintain strong relationships with customers to encourage repeat business and referrals.
Learn more about biomass pelletizing solutions
Start your pellet production line today
FAQs About Pellet Production Lines
-
What is a pellet production line?
A pellet production line is a series of machinery and equipment designed to process raw materials (such as biomass or feed) into pellets. This line typically includes equipment for crushing, drying, pelletizing, cooling, and packaging the pellets.
-
What types of raw materials can be used in a pellet production line?
A variety of raw materials can be used, depending on the type of pellets being produced. Common biomass materials include wood chips, sawdust, straw, rice husks, and agricultural residues. For feed pellets, common materials include grains, corn, soybean meal, and other agricultural by-products.
-
What are the key components of a pellet production line?
The main components of a pellet production line include:
Hammer Mill: For crushing raw materials into smaller particles.
Dryer: For reducing the moisture content of raw materials.
Pellet Mill: For compressing the dried materials into pellets.
Cooler: For cooling down the hot pellets after production.
Sifter: For separating finished pellets from fines and ensuring uniform size.
Bagging Machine: For packaging the pellets into bags for storage and transport. -
How does the pellet production process work?
Several factors influence pellet quality, including:
Moisture Content: Proper moisture content is crucial for producing high-quality pellets. Too much moisture can lead to poor pellet formation, while too little can cause excessive dust and poor binding.
Raw Material Size: The size of the raw material particles should be uniform to ensure consistent pellet quality.
Compression Ratio: The compression ratio of the pellet mill die should match the raw material characteristics.
Additives: Sometimes, binding agents or additives are used to improve pellet quality and durability. -
What factors affect the quality of pellets?
Several factors influence pellet quality, including:
Moisture Content: Proper moisture content is crucial for producing high-quality pellets. Too much moisture can lead to poor pellet formation, while too little can cause excessive dust and poor binding.
Raw Material Size: The size of the raw material particles should be uniform to ensure consistent pellet quality.
Compression Ratio: The compression ratio of the pellet mill die should match the raw material characteristics.
Additives: Sometimes, binding agents or additives are used to improve pellet quality and durability.
-
What is the ideal moisture content for pelletizing?
The ideal moisture content for pelletizing generally ranges between 10% and 15%. This ensures optimal pellet formation and quality.
-
How do I choose the right pellet mill for my needs?
Consider the following factors when choosing a pellet mill:
Capacity: Determine the required production capacity (e.g., kg/hour or tons/hour).
Raw Material: Consider the type of raw material you will be using and ensure the pellet mill is suitable for processing it.
Power Requirements: Ensure your facility can meet the power requirements of the pellet mill.
Pellet Size: Choose a pellet mill that can produce the desired pellet size and shape. -
What maintenance is required for a pellet production line?
Regular maintenance is crucial to ensure efficient operation and longevity of the equipment. Key maintenance tasks include:
Regular Cleaning: Clean the equipment regularly to prevent build-up and blockages.
Lubrication: Lubricate moving parts to reduce friction and wear.
Inspection and Replacement: Regularly inspect and replace worn or damaged parts, such as dies, rollers, and bearings. -
What safety precautions should be taken when operating a pellet production line?
Safety is paramount when operating a pellet production line. Key precautions include:
Training: Ensure all operators are properly trained in the safe operation and maintenance of the equipment.
PPE: Provide and enforce the use of personal protective equipment (PPE), such as gloves, goggles, and ear protection.
Emergency Procedures: Establish and practice emergency shutdown procedures and first aid measures.
Fire Safety: Implement fire safety measures, as dust from raw materials can be highly flammable. -
Can a pellet production line be customized?
Yes, pellet production lines can be customized to meet specific production requirements. Customization options may include:
Equipment Selection: Choose specific types of equipment based on the raw material and desired pellet characteristics.
Production Capacity: Tailor the line to achieve the desired production capacity.
Automation Level: Customize the level of automation based on the available workforce and production efficiency goals.